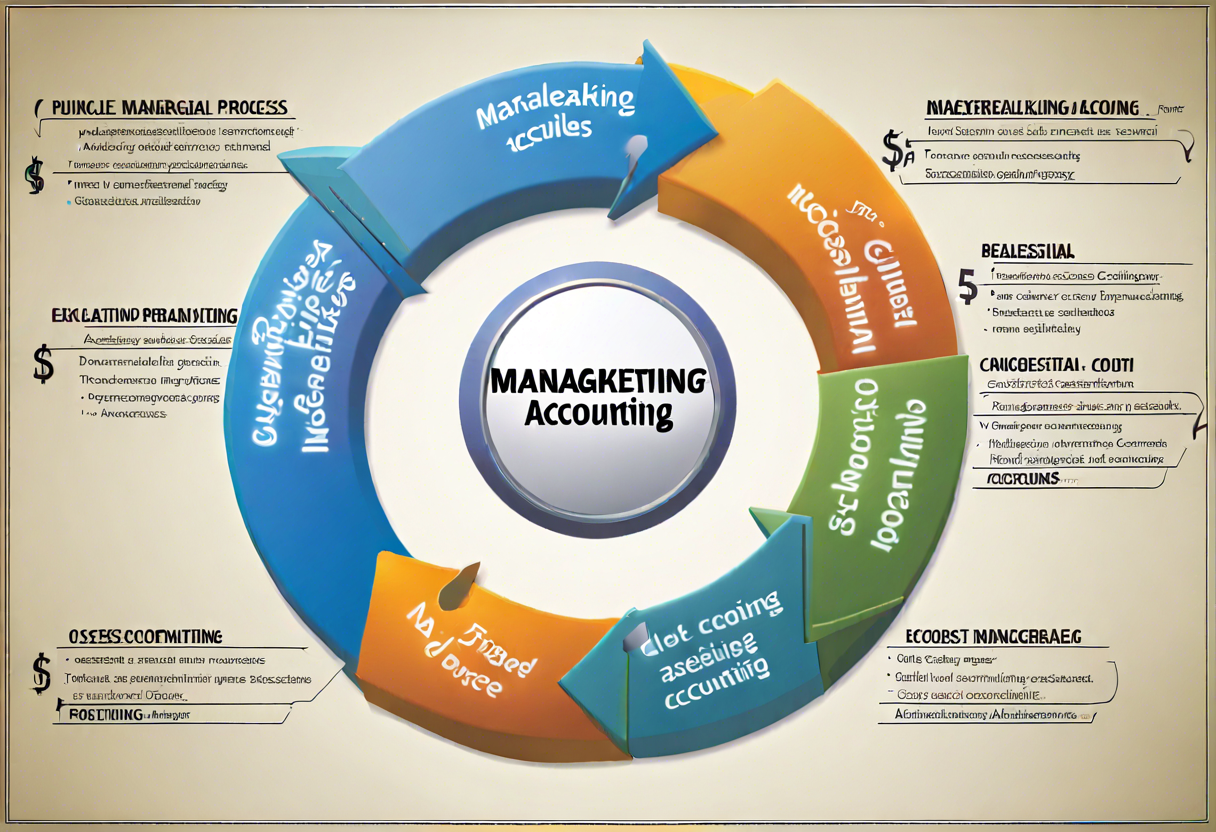
Managerial accounting process costing: Understanding the fundamentals and applications
Managerial accounting process costing encompasses a crucial aspect of financial management within organizations. Understanding the fundamentals and applications of process costing is essential for businesses to accurately allocate costs, evaluate performance, and make informed decisions. This article delves into the intricacies of managerial accounting process costing, shedding light on its significance and practical implications.
Importance of Managerial Accounting Process Costing
Managerial accounting process costing plays a pivotal role in determining the cost of production for goods or services in a manufacturing environment. By breaking down costs into various components and tracking them throughout the production process, businesses can ascertain the total cost incurred at each stage. This detailed cost information is instrumental in pricing decisions, budgeting, and assessing the profitability of different product lines.
Key Components of Process Costing
In the realm of managerial accounting, process costing involves analyzing direct materials, direct labor, and overhead costs associated with each production stage. Direct materials refer to the raw materials directly used in manufacturing a product, while direct labor pertains to the wages of workers directly involved in production. Overhead costs encompass all other indirect expenses, such as utilities and depreciation, that contribute to the manufacturing process.
Methods of Allocating Costs
There are various methods employed in managerial accounting process costing to allocate costs efficiently. For instance, the Weighted Average Costing method calculates the average cost of production by considering the beginning work in process inventory alongside current production costs. On the other hand, the First-In-First-Out (FIFO) method assumes that units produced first are sold or completed first, thereby influencing cost calculations accordingly.
Application in Decision Making
The insights derived from managerial accounting process costing are instrumental in guiding strategic decision-making within organizations. By analyzing cost trends, identifying cost drivers, and evaluating cost efficiency, businesses can optimize their production processes, streamline operations, and enhance overall profitability. Process costing data also aids in setting competitive prices that align with cost structures while ensuring a reasonable profit margin.
Continuous Improvement and Cost Control
One of the primary objectives of leveraging process costing in managerial accounting is to facilitate continuous improvement and cost control. By closely monitoring costs, identifying areas of inefficiency, and implementing corrective measures, businesses can enhance productivity, reduce wastage, and ultimately boost their bottom line. Process costing serves as a valuable tool for cost management and performance evaluation, enabling companies to stay agile and competitive in dynamic market environments.
Managerial accounting process costing is an indispensable mechanism for businesses to track, allocate, and analyze costs in a manufacturing environment. By understanding the fundamentals and applications of process costing, organizations can make informed financial decisions, improve operational efficiency, and drive sustainable growth. Embracing process costing as a cornerstone of financial management empowers businesses to navigate complexities, optimize resource utilization, and achieve long-term success in today’s competitive landscape.
Key differences between process costing and job order costing in managerial accounting
Managerial accounting plays a crucial role in helping organizations make informed business decisions by providing detailed financial information and analysis. Two common costing systems used in managerial accounting are process costing and job order costing. While both methods are used to determine the cost of producing a product or service, they differ in their approach and application within different types of industries.
Process Costing
Process costing is a method used to determine the cost of producing similar products on a large scale. This costing system is often employed in industries where products are manufactured in a continuous process, such as food processing, chemical manufacturing, and oil refining. In process costing, the total cost of production is spread out evenly over the total number of units produced during a specific period.
One of the key features of process costing is that it is best suited for industries where goods are produced in a continuous flow and where it is challenging to track the cost of each individual unit. This method is ideal for products that are homogenous and where the production process is standardized.
Job Order Costing
On the other hand, job order costing is used in industries where products are produced based on specific customer orders or specifications. This method is commonly found in industries like construction, custom manufacturing, and service industries where each job or project is unique and requires tracking costs separately.
Job order costing involves assigning costs to each job or project based on the materials, labor, and overhead expenses incurred during production. This method allows for a more detailed analysis of the cost of each individual unit produced, making it beneficial for industries with custom or unique products.
Key Differences
The primary difference between process costing and job order costing lies in the way costs are accumulated and assigned to products. In process costing, costs are averaged over the total number of units produced during a specific period, leading to a uniform cost per unit. On the other hand, job order costing traces actual costs incurred for each job or project, resulting in a specific cost per unit based on the requirements of that particular job.
Another key difference is the level of detail and tracking involved in each costing method. Process costing provides a broader overview of costs incurred during the production process, making it more suitable for industries with standardized products. In contrast, job order costing offers a more granular view of costs by tracking expenses at the individual job or project level, making it ideal for industries with customized or unique products.
Both process costing and job order costing are essential tools in managerial accounting that help businesses determine the cost of production. Understanding the key differences between these two costing methods is crucial for businesses to choose the most appropriate costing system based on their industry, production process, and product customization requirements. By selecting the right costing method, businesses can accurately calculate costs, make informed pricing decisions, and ultimately improve their overall financial performance.
The role of cost accounting systems in enhancing managerial decision-making
Cost accounting systems play a crucial role in providing valuable information to managers for making informed decisions within an organization. These systems are designed to track, record, and analyze the various costs associated with production activities. By leveraging cost accounting data, managers can evaluate performance, determine product pricing, assess profitability, and identify areas for cost reduction. Let’s explore how cost accounting systems contribute to enhancing managerial decision-making.
Importance of Cost Accounting Systems
Cost accounting systems help managers understand the true cost of producing goods or services. By categorizing costs into direct and indirect costs, as well as fixed and variable costs, these systems provide a clear picture of cost behavior within the organization. This insight is essential for making pricing decisions, setting performance targets, and optimizing resource allocation.
Cost Control and Performance Evaluation
One of the primary purposes of a cost accounting system is to assist in cost control and performance evaluation. Managers can compare actual costs against budgeted costs to identify any variances requiring attention. By analyzing these discrepancies, managers can take corrective actions to improve efficiency, reduce waste, and enhance overall performance.
Strategic Decision-Making
Cost accounting systems enable managers to make strategic decisions that align with the organization’s goals and objectives. Whether it’s introducing a new product line, discontinuing a low-profit product, or investing in new technology, cost accounting data provides the necessary insights to evaluate the financial implications of such decisions. This strategic approach helps organizations remain competitive and agile in a dynamic business environment.
Product Pricing and Profitability Analysis
Setting the right price for products or services is crucial for ensuring profitability. Cost accounting systems help managers determine the full cost of production, including direct materials, labor, and overhead costs. By adding a markup to cover desired profit margins, managers can establish competitive prices that also contribute to the organization’s bottom line.
Cost Reduction and Efficiency Improvements
Identifying opportunities for cost reduction and efficiency improvements is a continuous process in any organization. Cost accounting systems play a vital role in highlighting areas where costs can be controlled, waste minimized, and processes optimized. By analyzing cost trends and performance metrics, managers can implement strategies to enhance operational efficiency and maximize profitability.
Cost accounting systems serve as a fundamental tool for enhancing managerial decision-making within organizations. By providing accurate and timely cost information, these systems empower managers to evaluate performance, control costs, make strategic decisions, and improve overall profitability. Investing in a robust cost accounting system is essential for organizations looking to drive efficiency, competitiveness, and financial success.
Implementing activity-based costing to optimize cost allocation in managerial accounting
Implementing Activity-Based Costing for Optimized Cost Allocation in Managerial Accounting
Activity-based costing (ABC) is a strategic approach used in managerial accounting to allocate costs more accurately by identifying activities that consume resources. This method provides a detailed breakdown of costs, enabling a more precise understanding of the factors driving expenses within an organization. By implementing ABC, businesses can optimize cost allocation, improve decision-making processes, and enhance overall financial performance.
Understanding Activity-Based Costing Process
The first step in implementing ABC is to comprehend the process involved. Traditional costing methods often allocate overhead costs based on a single cost driver, such as direct labor hours or machine hours. However, ABC recognizes that activities, not just volume measures, drive these costs. By identifying the specific activities that consume resources, ABC assigns costs more accurately to the products or services that benefit from them.
Identifying Cost Drivers and Activities
In ABC, cost drivers are the factors that directly influence the cost of an activity. By identifying these drivers, businesses can allocate costs more effectively. Activities are then categorized based on their cost drivers, allowing for a granular analysis of expenses. This detailed breakdown enables managers to pinpoint areas where costs can be reduced or optimized, leading to a more efficient allocation of resources.
Allocating Costs to Products or Services
Once cost drivers and activities are identified, ABC allocates costs to individual products or services based on their consumption of resources. This method contrasts with traditional costing systems that may over or under allocate overhead costs. By accurately assigning costs to specific outputs, businesses gain a clearer picture of the true profitability of each product or service, enabling informed pricing decisions and resource allocation.
Enhancing Decision-Making Processes
Implementing ABC enhances decision-making processes by providing managers with valuable insights into cost structures. By understanding the true cost of activities and how they relate to products or services, managers can make data-driven decisions to improve efficiency and profitability. ABC enables a more precise analysis of costs, allowing for targeted cost reduction initiatives and strategic investments.
Improving Financial Performance
Optimizing cost allocation through ABC ultimately leads to improved financial performance. By accurately tracing costs to products or services, businesses can eliminate inefficiencies, reduce waste, and enhance overall profitability. The insight provided by ABC empowers managers to make informed decisions that positively impact the bottom line, contributing to sustainable growth and long-term success.
Implementing activity-based costing in managerial accounting is a strategic approach to optimize cost allocation. By understanding the ABC process, identifying cost drivers and activities, allocating costs accurately, enhancing decision-making processes, and improving financial performance, businesses can achieve greater efficiency and profitability. ABC provides a comprehensive framework for businesses to allocate costs more effectively, leading to enhanced competitiveness and strategic advantage in today’s dynamic business environment.
Strategic cost analysis and decision-making for managers: A comprehensive guide
Understanding Strategic Cost Analysis and Decision-Making for Managers
In today’s rapidly evolving business landscape, strategic cost analysis plays a pivotal role in the decision-making process for managers across various industries. By closely examining costs and their impact on operations, companies can make informed choices that drive profitability and sustainability in the long run. This comprehensive guide delves into the importance of strategic cost analysis and provides insights into how managers can leverage this information to make data-driven decisions.
The Significance of Strategic Cost Analysis
Strategic cost analysis involves a detailed assessment of the expenses incurred by a company in its day-to-day operations. It goes beyond simply tracking costs to understanding the drivers behind these expenses and how they align with the organization’s strategic objectives. By conducting a thorough cost analysis, managers can identify areas of inefficiency, uncover cost-saving opportunities, and optimize resource allocation.
Utilizing Cost Data for Decision-Making
Cost data serves as a valuable tool for managers when making critical decisions that impact the company’s performance. By leveraging cost information, managers can assess the profitability of products or services, evaluate the financial implications of different strategic initiatives, and set prices that align with both market dynamics and internal cost structures. Additionally, cost analysis enables managers to forecast future expenses accurately and create budgets that reflect the organization’s financial goals.
Cost-Volume-Profit Analysis
One of the essential tools in strategic cost analysis is Cost-Volume-Profit (CVP) analysis. CVP analysis helps managers understand the relationship between costs, sales volume, and profit levels. By using this framework, managers can determine break-even points, evaluate the impact of different pricing strategies, and assess the overall financial viability of a business venture. CVP analysis provides valuable insights that guide decision-making around production levels, pricing decisions, and sales strategies.
Activity-Based Costing
Another valuable technique in strategic cost analysis is Activity-Based Costing (ABC). ABC assigns costs to specific activities within an organization, providing a more accurate understanding of the resources consumed by each process. By adopting ABC, managers can identify cost drivers, allocate overhead expenses more effectively, and pinpoint areas where process improvements can lead to cost savings. This granular view of costs enables managers to make strategic decisions that maximize efficiency and drive profitability.
Strategic Cost Management for Sustainable Growth
Strategic cost analysis is a fundamental aspect of decision-making for managers seeking sustainable growth and profitability. By harnessing cost data, leveraging tools like CVP analysis and ABC, and adopting a strategic approach to cost management, managers can optimize performance, boost competitiveness, and ensure long-term success for their organizations. Strategic cost analysis empowers managers to make informed decisions that drive value creation and foster a culture of financial prudence and efficiency.
Conclusion
In today’s dynamic business environment, managerial accounting plays a vital role in helping organizations understand, analyze, and control their costs effectively. Through the process costing method, businesses can gain valuable insights into the cost of production at each stage of the manufacturing process. By breaking down expenses into specific units or departments, managers can make informed decisions to enhance operational efficiency and profitability.
Understanding the fundamentals and applications of managerial accounting process costing is essential for businesses looking to maintain a competitive edge in the market. By accurately allocating costs to each production stage, organizations can identify areas for improvement, streamline processes, and eliminate inefficiencies. This granular approach to cost analysis enables managers to make data-driven decisions that drive sustainable growth and success.
When comparing process costing to job order costing, it’s crucial to recognize the key differences between the two methods. While job order costing is suitable for customized products or services with distinct characteristics, process costing is ideal for standardized goods produced in large quantities. By selecting the appropriate costing method based on the nature of the products or services, managers can ensure accurate cost calculations and optimize resource utilization.
Cost accounting systems play a pivotal role in providing managers with the necessary information to make informed decisions. These systems help track, analyze, and allocate costs to different cost objects, enabling managers to evaluate performance, set pricing strategies, and allocate resources effectively. By leveraging cost accounting systems, organizations can enhance their decision-making processes and improve overall financial performance.
Implementing activity-based costing (ABC) can further enhance cost allocation practices in managerial accounting. By identifying and assigning costs to specific activities that drive expenses, ABC offers a more accurate representation of the true cost of production. This detailed cost information allows managers to assess the profitability of products or services more precisely, identify cost drivers, and prioritize cost-saving initiatives.
Strategic cost analysis plays a pivotal role in managerial decision-making, providing managers with insights into the cost structure of the organization and its impact on profitability. By conducting comprehensive cost analyses, managers can identify areas of cost inefficiency, benchmark performance against industry standards, and develop strategic initiatives to improve financial outcomes. Strategic cost analysis empowers managers to make informed decisions that align with the organization’s long-term goals and objectives.
Mastering the principles of managerial accounting process costing is essential for driving business success in today’s competitive landscape. By understanding the nuances of process costing, recognizing the differences between costing methods, leveraging cost accounting systems, implementing activity-based costing, and conducting strategic cost analyses, managers can enhance their decision-making processes and achieve sustainable growth. Through a strategic focus on cost optimization and efficiency, organizations can position themselves for long-term success and profitability in an ever-evolving business environment.